Tool-Temp devices strengthen core competence of Sidrag AG
Tool-Temp devices strengthen core competence of Sidrag AG
Tool-Temp AG spoke with Eugen Vigini, Managing Director, and Luis Gil, Foundry Manager, about the temperature control of casting tools. The challenges in the production process and developments in the industry were also discussed.
Sidrag AG is known as an experienced supplier for small and medium series in Switzerland. Based in Baar, Switzerland, they have been successfully producing die-cast components made of aluminum, magnesium and zinc alloys from a single source for many years. In 1998, the range was expanded to include the multifaceted material magnesium. Sidrag AG was honoured with the Innovation Award by the Canton of Zug for this successful pioneering achievement. Sidrag AG is characterised by outstanding quality, flexibility, short response times and just-in-time deliveries. In addition, the company takes care of the entire implementation of the value chain for the components in question.
The experienced supplier Sidrag AG has been one of Tool-Temp’s valued customers for more than 25 years. Over 13 temperature control units are in daily use in the die casting foundry. “Simplicity, trouble-free, user-friendly, the units are optimally integrated into the manufacturing process” says Luis Guil, Foundry Manager at Sidrag AG.
Tool-Temp devices optimise and stabilise the manufacturing process for Sidrag’s most important industrial sectors, such as medical technology, measurement technology, optics, the construction supply industry, sensor technology, and the electrical and electronics sectors. An extremely positive development has been seen in recent years in lightweight construction, namely optics and medical technology.
Mega- or gigacasting – the production of oversized die-cast parts – is becoming increasingly important in the automotive industry, especially in vehicle body construction. However, this does not affect Sidrag, which specialises in the production of small and medium series outside of the highly competitive automotive sector. The focus lies on the development and optimisation of the classic casting cell. Throughout the casting process, the equipment is networked with peripheral devices, resulting in increased automation. This substantially increases productivity, reduces costs and creates a 30 % higher degree of staff independence so that freed-up time can be used elsewhere. Another advantage of a higher degree of automation is more consistent production processes with optimised cycle times, less waste and thus a high quality standard.
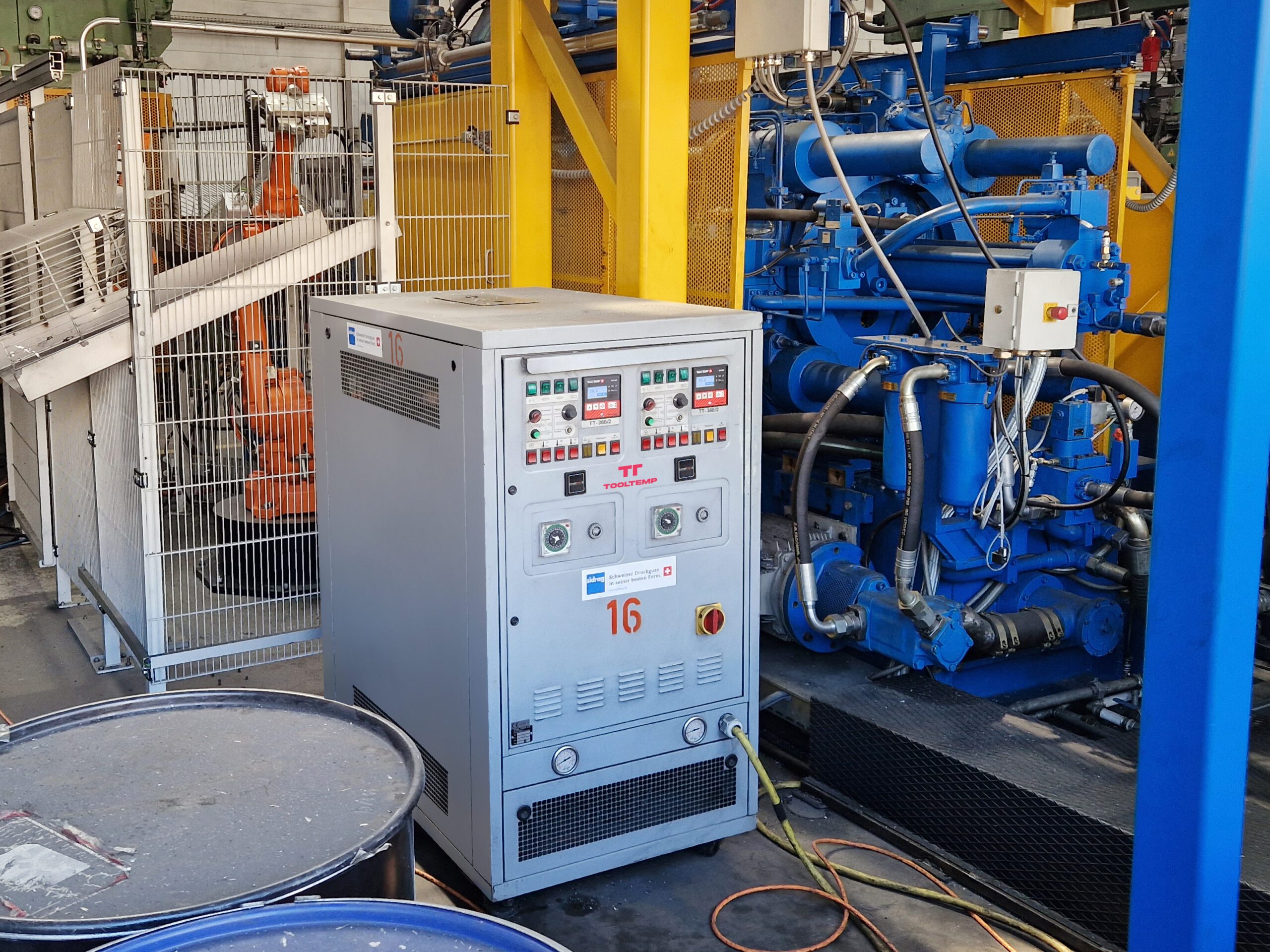
Sidrag AG uses very small die-casting moulds with sizes from 200 x 200 x 200 mm to 800 x 800 x 800 mm. Parts with weights of 3 – 4 g up to max. 3 – 4 kg are produced. The units are used for tempering mould inserts, mould frames, slides and nozzles.
Sidrag’s challenge and core competence is its huge knowledge in the casting process and the processing of aluminium, zinc and magnesium. Sidrag is particularly challenged in the production of magnesium components; this is because liquid magnesium with a melt temperature of 650 °C hardens twice as fast as aluminium and therefore requires a high flow rate. In order to achieve stable temperature control and good heat dissipation, it is essential to have higher mould temperatures and the largest possible mould channels to optimise flow. Therefore, eight 2-circuit oil temperature control units from Tool-Temp are used on several die casting machines. From different device generations, the TT-370/2, TT-380/2 to TT-388/2 perform at the highest level at continuous temperatures of 240 to 280 °C. The powerful and high-quality 2-circuit units guarantee stable temperature control and trouble-free continuous operation, even under tough everyday conditions, especially in the die-casting industry. The easy application of the units and their usability are appreciated by the employees. The equipment, which is fitted with time switches at the customer’s request, in addition to various other additional features, ensures an even greater user-friendliness. Thanks to the pre-programmed, autonomous unit start, the heating process is already complete by the beginning of the shift.
Tool-Temp offers customised solutions to optimise production processes. Especially for Sidrag’s magnesium application, five TT-168 E/PHE temperature control units were modified for operation with heat transfer oils. Here, only nozzles and individual slides are cooled between 20 – 40 °C. Due to the high melting temperatures of the magnesium of 620 – 640 °C, a very high cooling capacity is required to dissipate the heat.
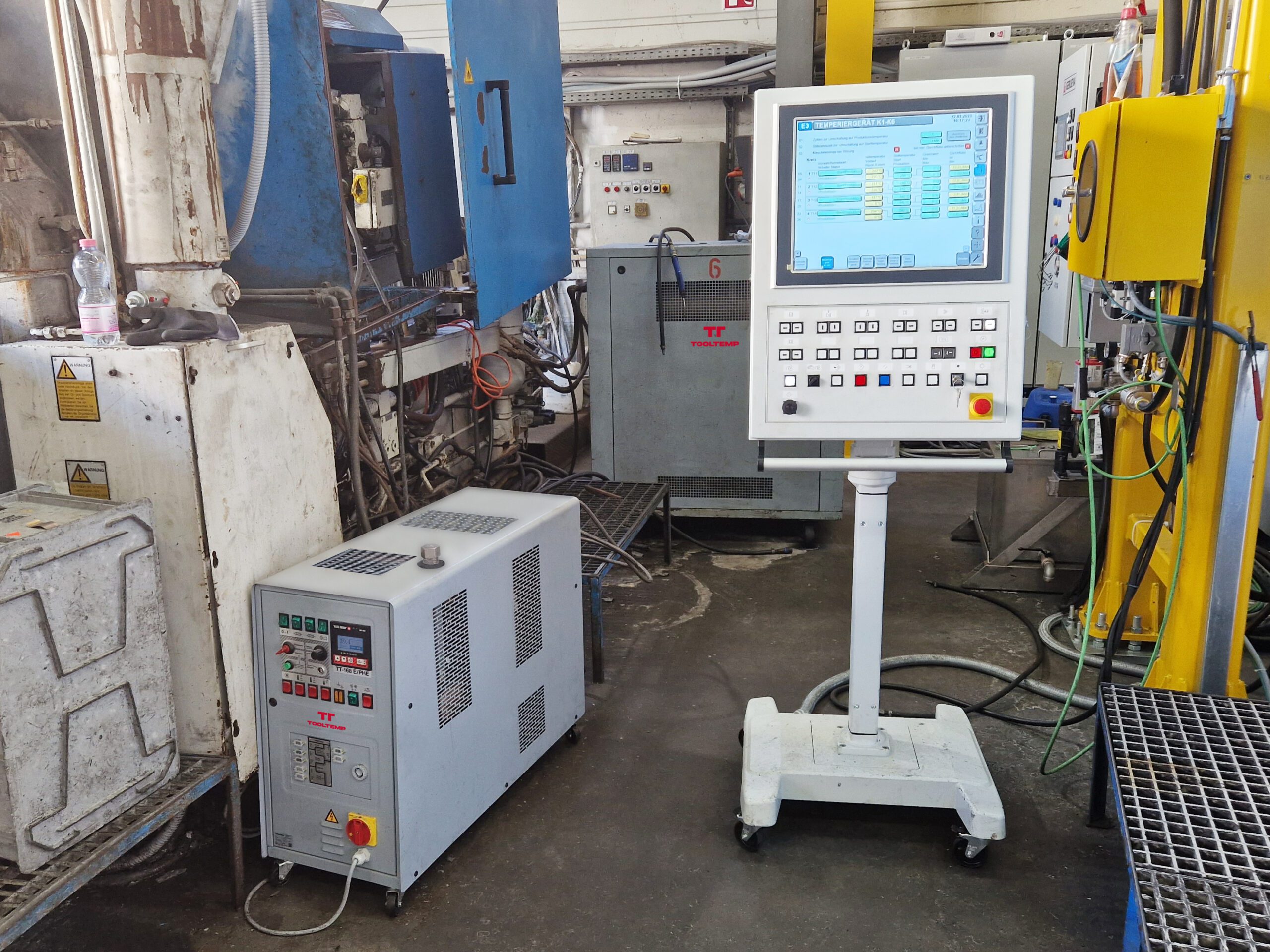
Tool-Temp supports its customers with comprehensive services from a single source. Sidrag AG is also very satisfied with the services, which fully meet their expectations. Particularly important are the short delivery routes, the permanent availability of spare parts with fast delivery times, as well as the fast response times with customised support and solution proposals.
“The geographical location of the company, the highly competent contacts who are available to us whenever we need them, either in the sales, service or spares departments had been instrumental in our long standing supplier customer relationship which continues to this day. The high quality materials and the experience with Tool-Temp equipment is unrivalled”, concluded Luis Gil.
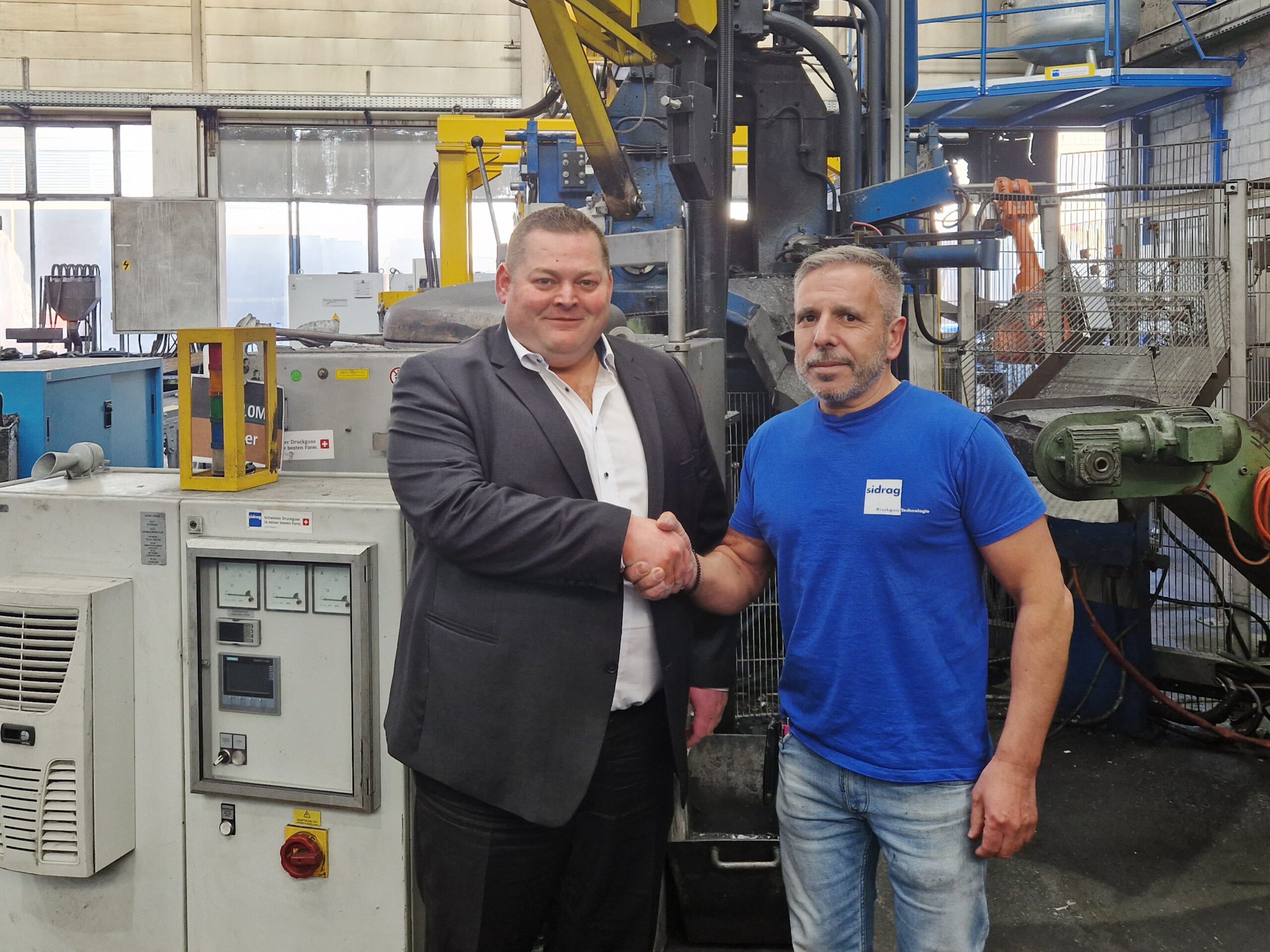
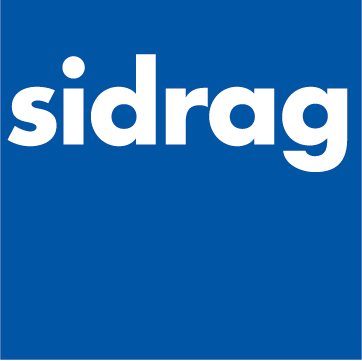
Macrocast GmbH relies on accurate and reliable Tool-Temp temperature control units
Macrocast GmbH relies on accurate and reliable Tool-Temp temperature control units
Tool-Temp spoke with Jens Paul, Technical Manager of Macrocast die casting foundry, about the tempering of their moulds, the challenges in the production process and the development in foundries.
Marcrocast GmbH is a specialized die casting foundry based in Samstagern on the upper side of Lake Zurich in Switzerland and is an affiliated company of Franz Binder GmbH & Co. El-ektrische Bauelemente KG in Neckarsulm, Germany. One of the core competences of this successful Swiss company is the production of complex zinc die cast components, mainly with mechanical CNC finishing, and specialises in the production of small components as well as small series. Macrocast is one of the renowned manufacturers for connectors with its vertical range of manufacture and produces most of the zinc die casting series for the Binder Group (65 %).
Tool-Temp AG is proud to count Macrocast among its valued customers for many years. Ten oil temperature control units are in daily use in this die casting foundry and recently a large TT-216’000 cooling unit with a nominal power capacity of 216 kW was put into operation for the entire die casting foundry. We visited Mr. Paul and asked him a few questions.
1. What exactly is being tempered at Macrocast?
Steel moulds weighing 120 – 180 kg are tempered. The temperature range to be covered is 90 °C for large- or thick-walled die castings, and up to 200 °C for very thin-walled die castings that require high and fast flow properties. An average of 4 parts per cycle are produced in the tool sizes used.
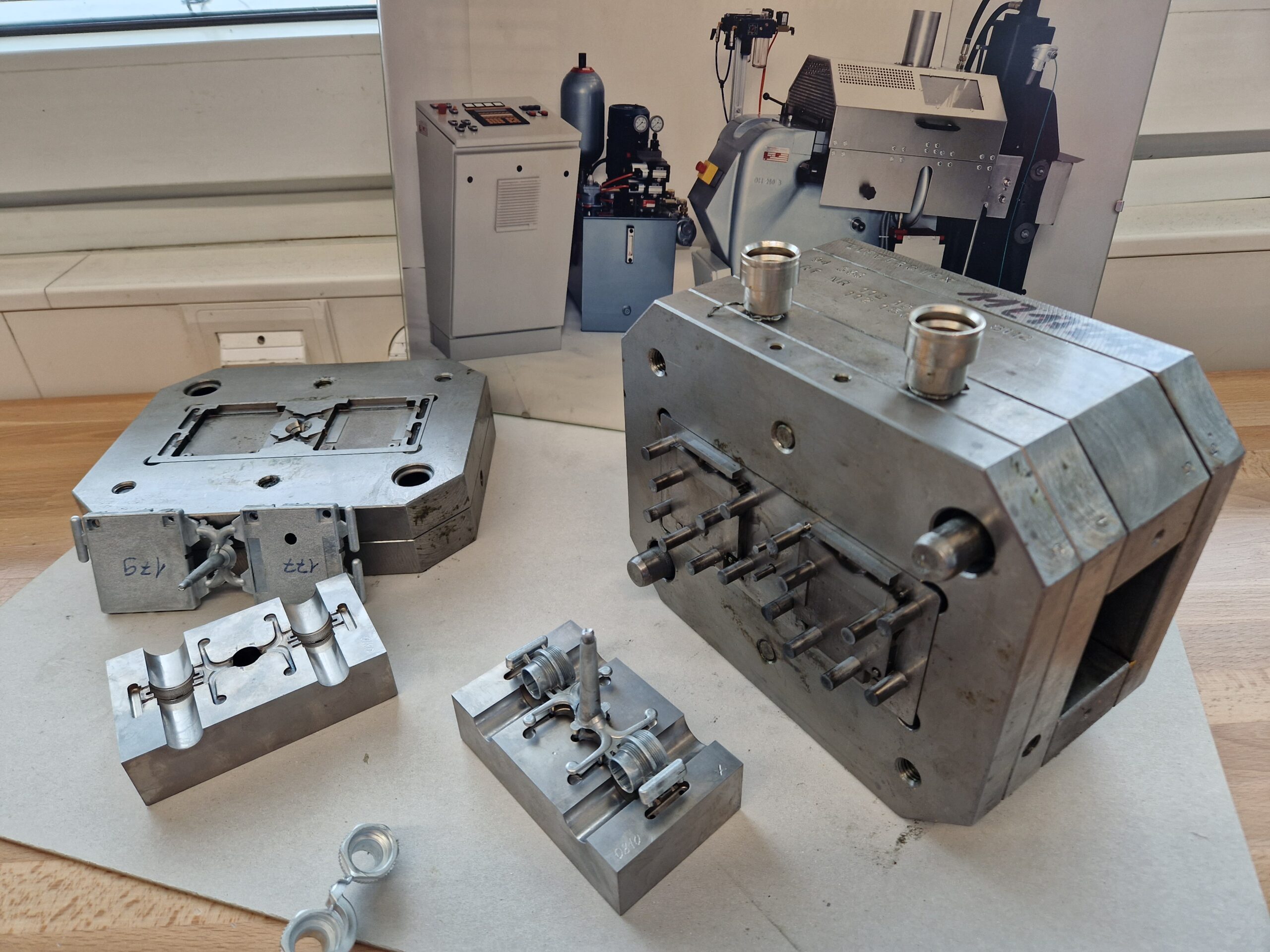
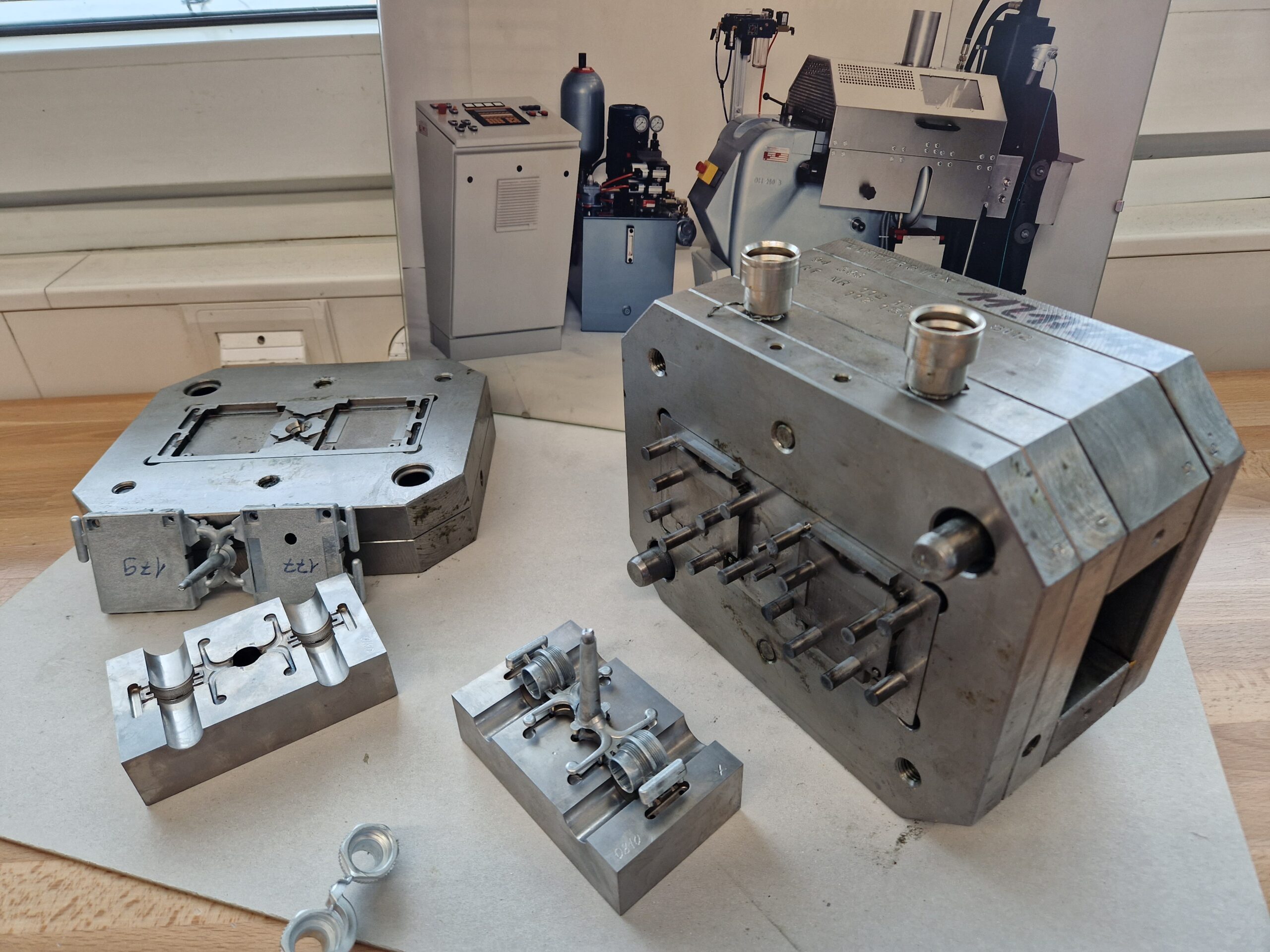
2. Zinc casting is suitable for countless applications, from simple window fittings to complex electronic components and automotive components to spectacle cases. To which industry do your biggest customers belong?
The die cast parts are mainly supplied to the electrical industry and drive technology. Brackets and fittings for doors or windows are also produced for the fastening industry.
60 – 70 % of these die cast parts are exported and approx. 30 % are produced for Swiss customers.
3. How has your industry and applications developed in recent years?
Many die casting foundries are following the trend and investing in Megacasting, the joining of several components into one die cast part. It has the potential to revolutionize the manufacturing process of automobiles. Since Macrocast specializes in small-series parts and produces small parts, Megacasting is not done. There are no such changes coming in the casting process for small parts. The more cavities a mould has, the greater the challenge to ensure that all castings in the same production cycle are cast in perfect and equal quality.
However, there is a clear trend towards connectivity. Connecting the temperature control unit to the machine control system simplifies the production process significantly and is indispensable in terms of quality assurance. The temperature controller ensures that the die cast parts are produced without quality problems.
4. In what way do Tool-Temp units simplify the production process in your die casting foundry?
The greatest risk in the production of die cast parts is material doubling, which can occur due to cold fronts during casting (too low casting speed leads to premature solidification). Especially with thin-walled castings, material doubling is particularly visible and cannot be accepted. The solidification temperature of zinc is 387 °C and therefore, Macrocast relies on Tool-Temp oil tempering units, by controlling at high temperatures.
Our goal is the continuous optimization of cycle times, and this is achieved by using the Tool-Temp oil temperature control units TT-248 (up to max. 200 °C), TT-288 / MP988 (up to max. 250 °C).
5. How many hours are the Tool-Temp units in use every day?
We use the units for 13 hours per day (at the end of the shift the units are switched off), but they can easily be used in 24/7 operation.
6. We are very grateful for our long-standing good business relationship. What brought you to Tool-Temp years ago?
More than 6 years ago, employees came across Tool-Temp through internet research. Since the focus was on independence, individual solutions, quick communication channels and fast availability of equipment and spare parts, it quickly became clear that Tool-Temp would become the business partner.
7. What are your experiences with the Tool-Temp units?
The temperature control units are very reliable, this is proven by their control accuracy. They easily withstand the rough everyday conditions in die casting.
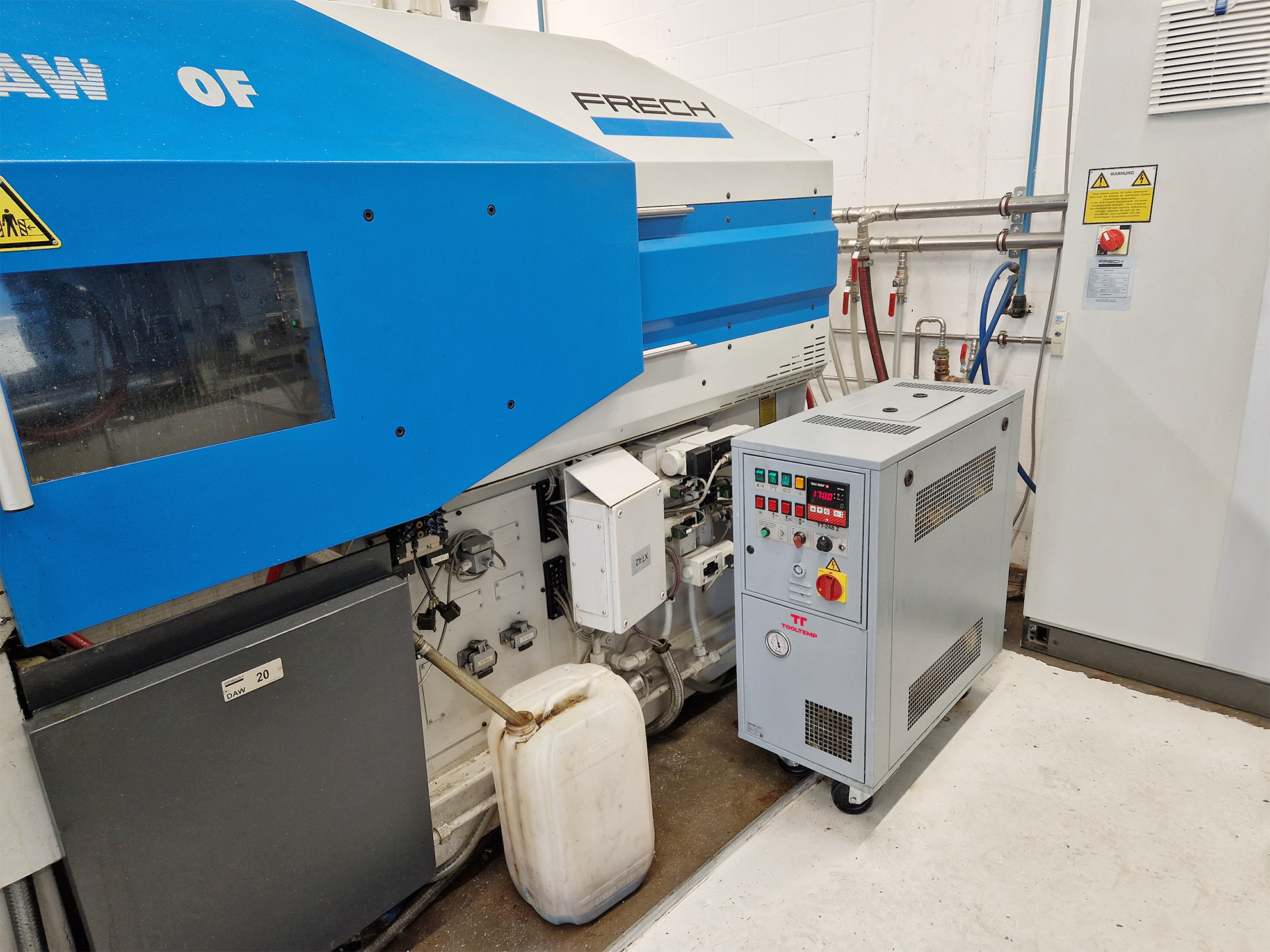
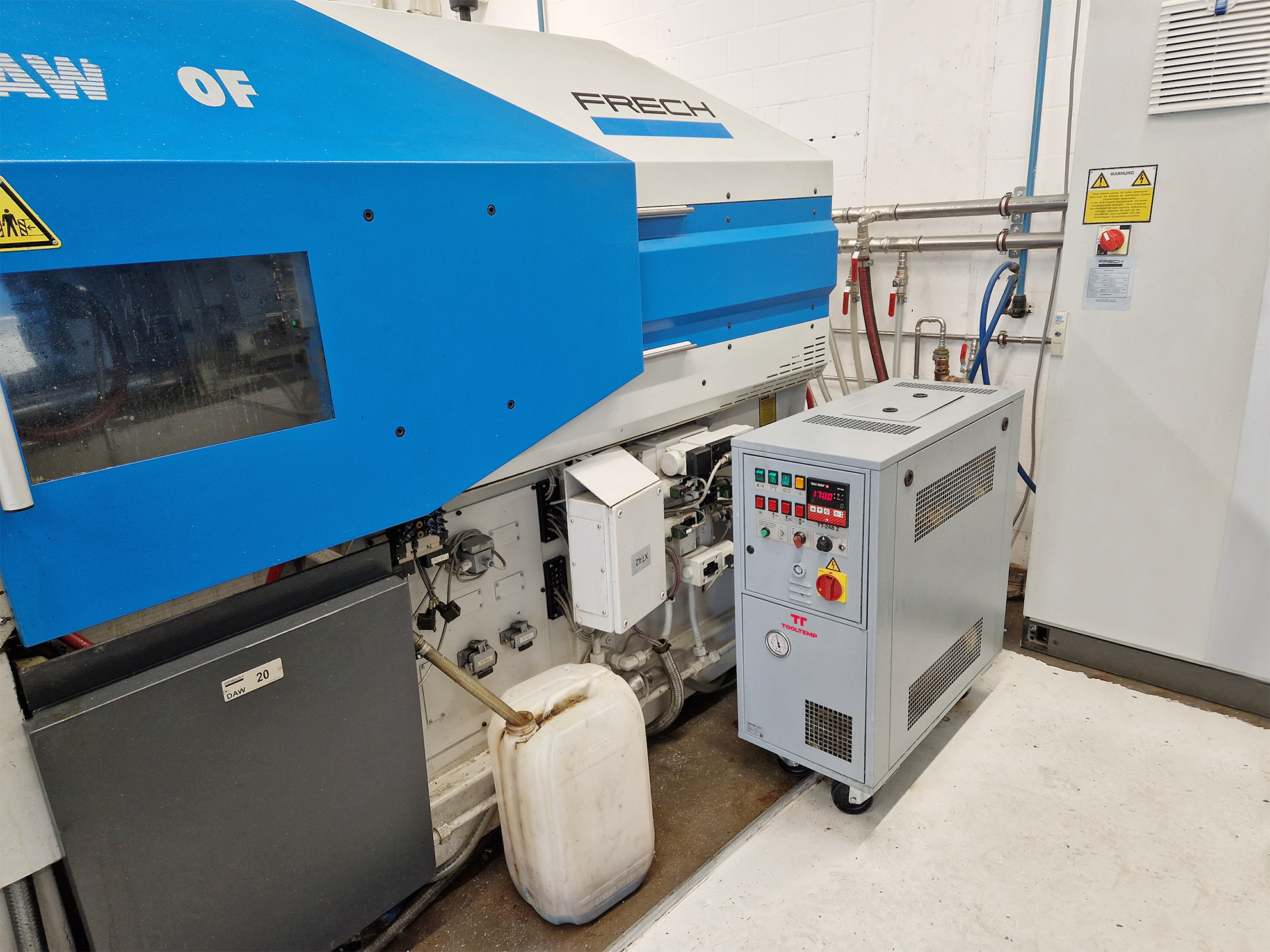
With very small cooling bore cross-sections, there is the difficulty of heat dissipation, and this can be easily compensated for by higher tool temperatures. Macrocast relies on the robust Tool-Temp oil temperature control units. The uncomplicated system design makes the units easy to operate.
8. Are you satisfied with the performance of the units and the Tool-Temp service?
We appreciate the very short reaction times and solutions from Tool-Temp-After-Sales and are pleased to confirm that we have not had any production downtimes with the use of Tool-Temp temperature control units.
We are very satisfied with the unit’s performance, consequently, when we wanted to mod-ernize our cooling system a year ago, it was also clear to us that Tool-Temp would offer a solution tailored to our requirements. Since then, the TT-216’000 cooling unit has provided the cooling water supply for the entire die casting system and all temperature control units.
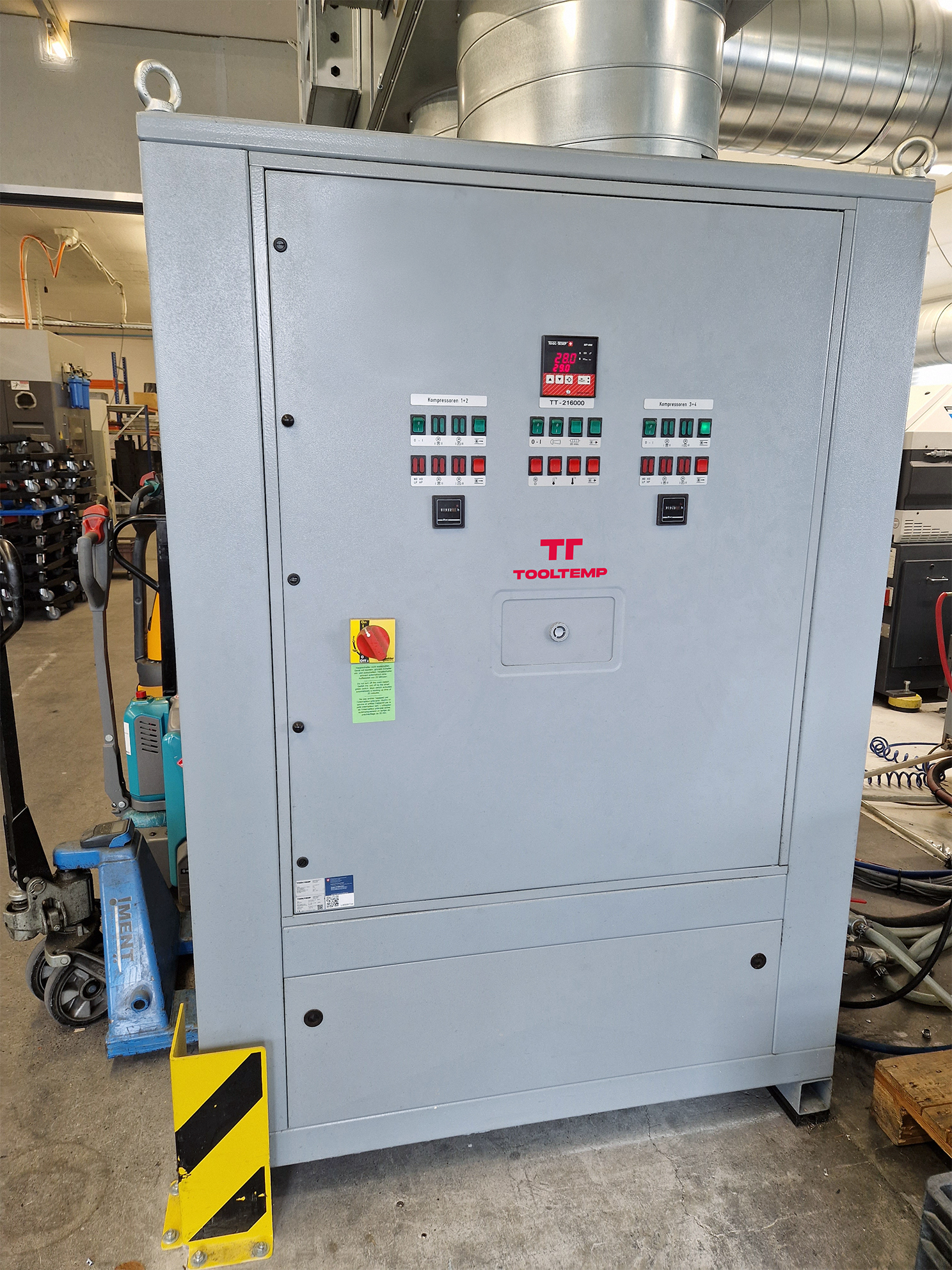
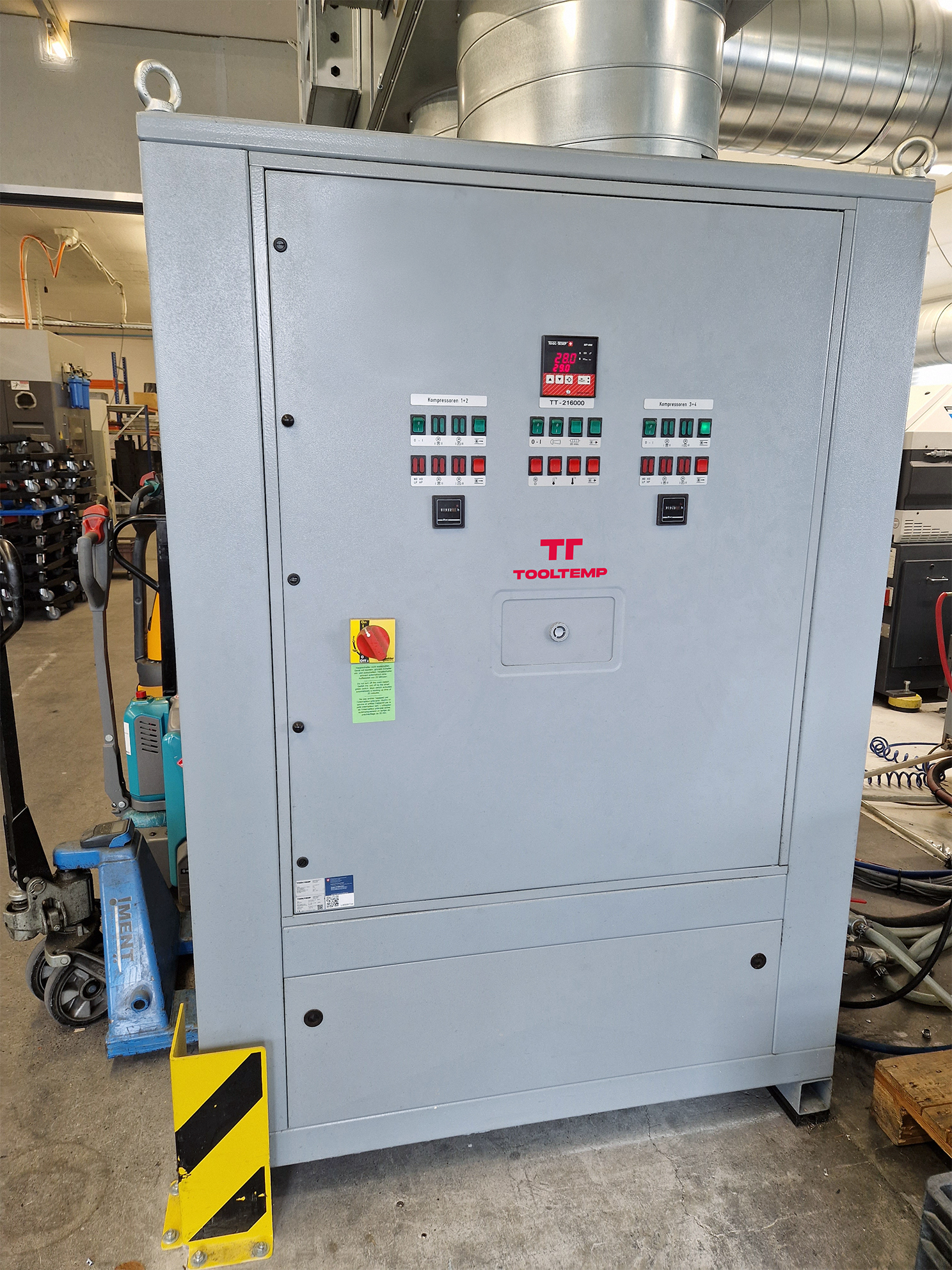
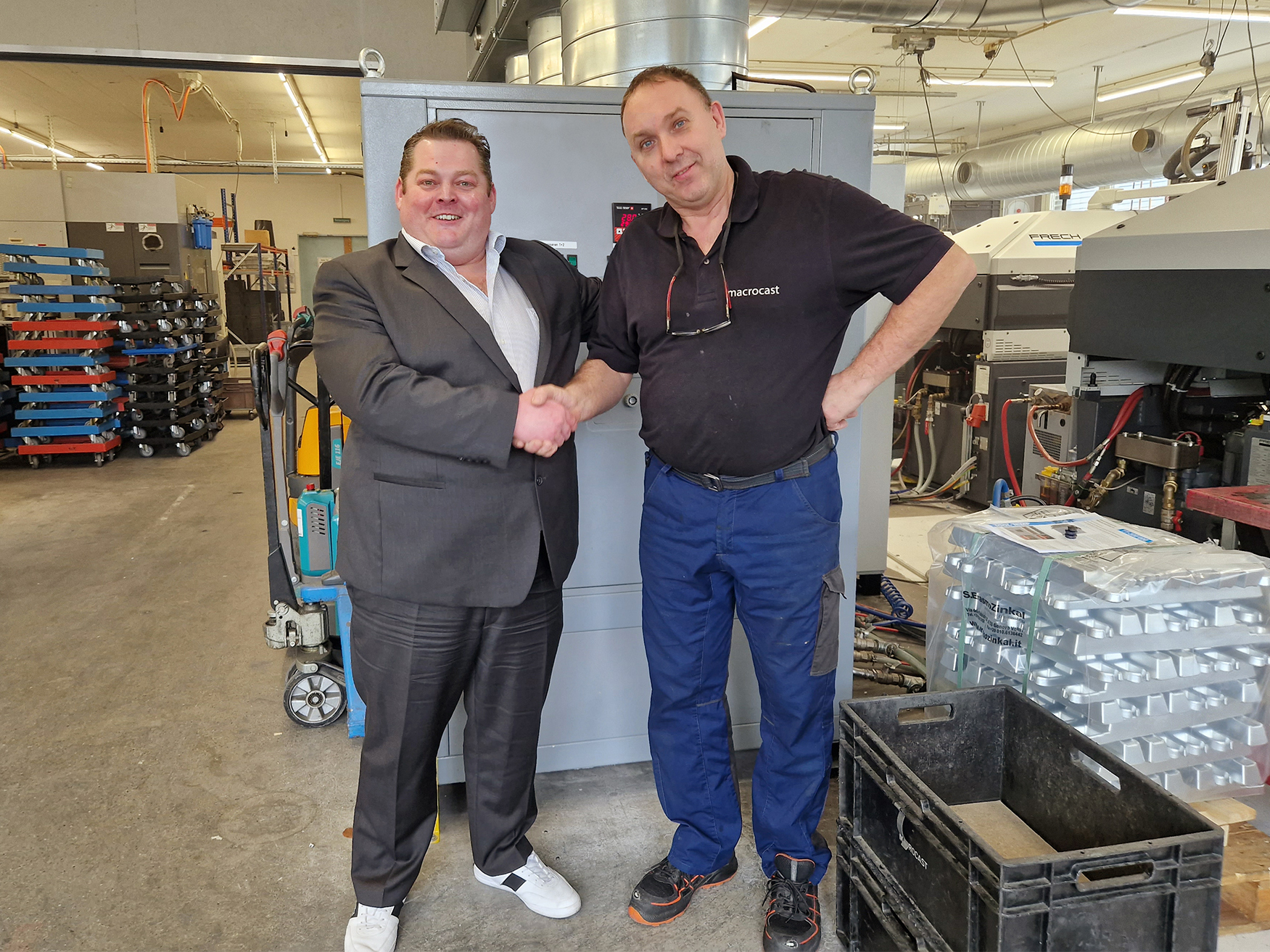
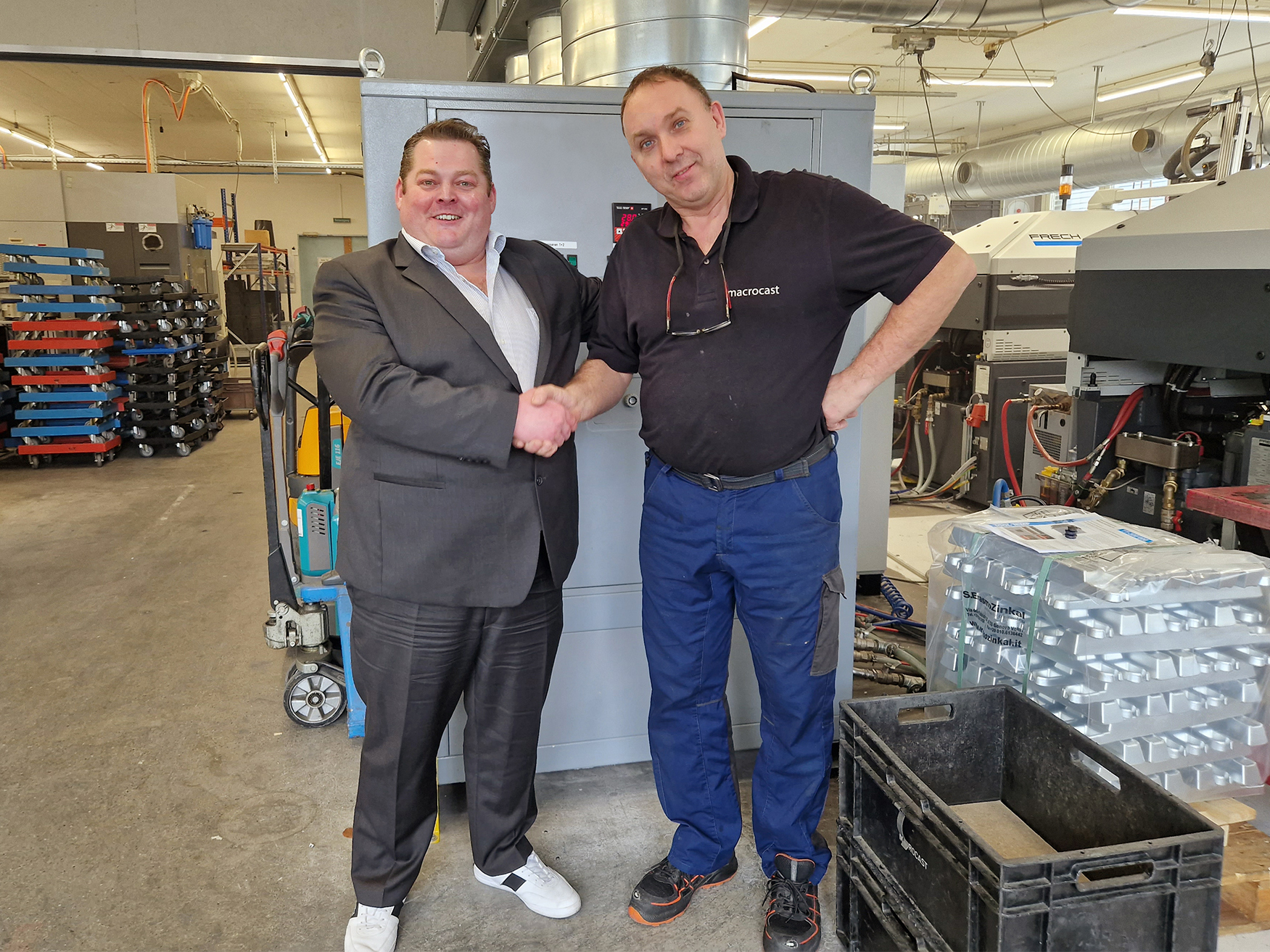
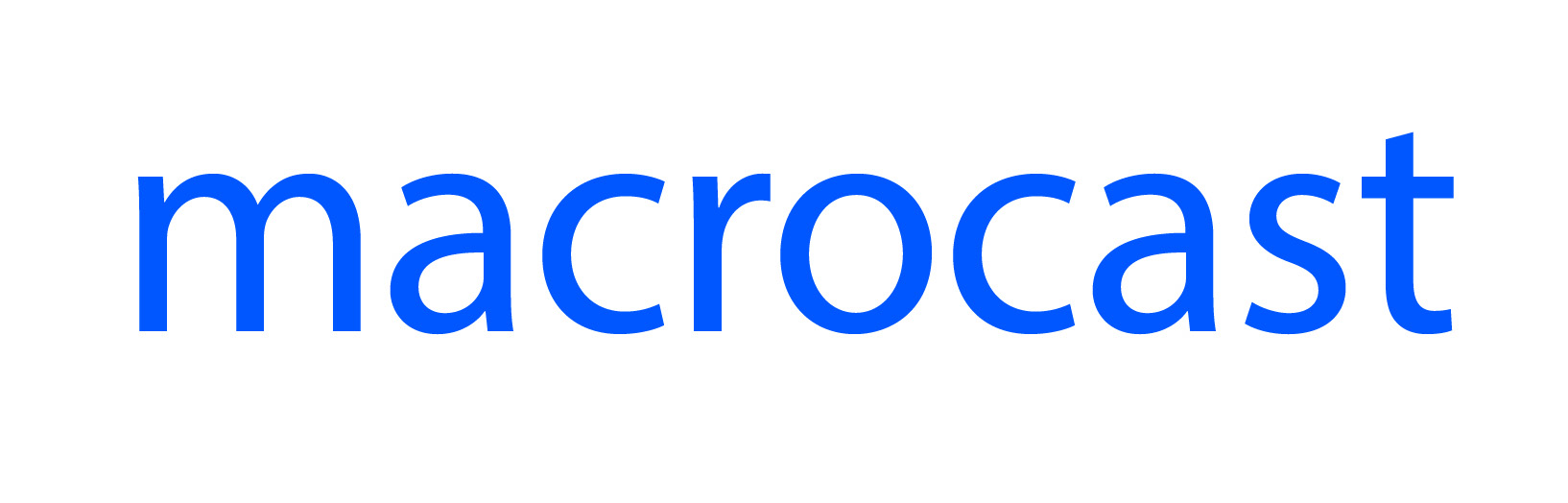
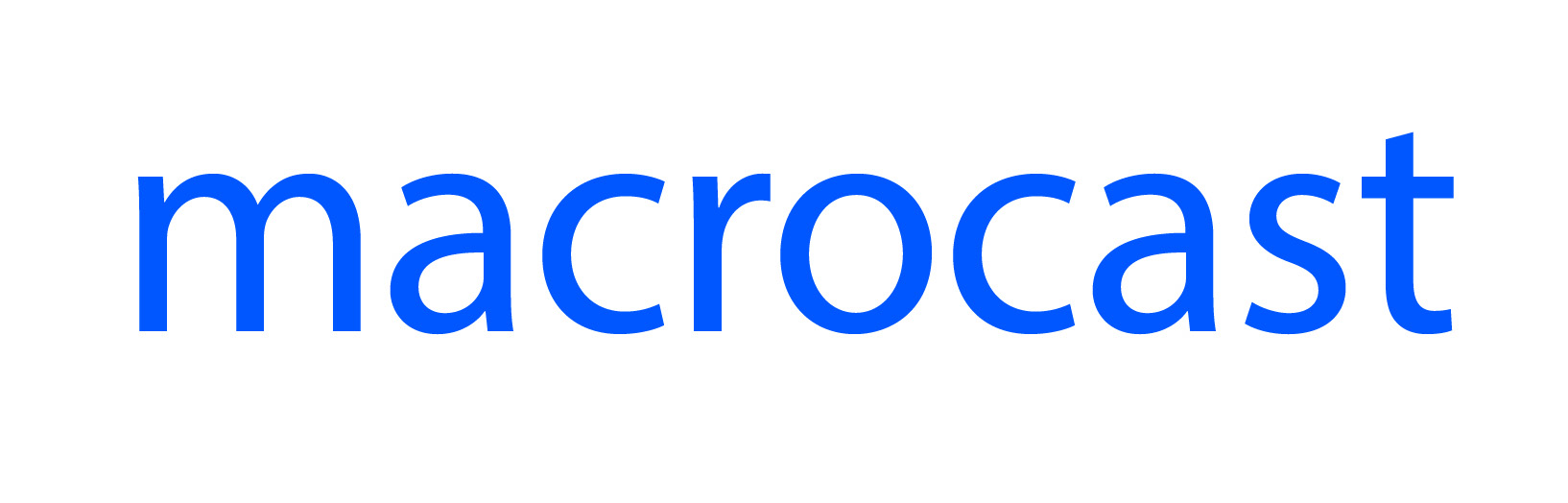
New management at Tool-Temp in the Czech Republic
The Swiss parent company Tool-Temp AG informs about an important mutation in the Czech subsidiary Tool-Temp CZ s.r.o., in Zubří/Czech Republic. As of February 1, 2023, Mr. Petr Čmelík will take over the operational management as the new Managing Director.
Lukáš Devera as President of the Board of Directors and current operational manager of Tool-Temp CZ s.r.o. hands over the operational management to Petr Čmelík. However, Lukáš Devera will continue to assist Mr. Petr Čmelík, as the new Managing Director, in an advisory capacity as Chairman of the Board of Directors.
Petr Čmelík has been working at Tool-Temp CZ s.r.o., in Zubří/Czech Republic for 2 years. He has 17 years of experience in plastic injection molding, blow molding and tooling and has been instrumental in the company’s success. As of February 1, 2023, he will officially take over the operational management of Tool-Temp CZ s.r.o. as Managing Director and will serve the Czech and Slovak markets with temperature control and cooling equipment.
“The company Tool-Temp AG would like to thank Lukáš Devera for his contribution to the company, especially in the establishment of the company as well as its successful development. At this point we wish Petr Čmelík a lot of success in his new position and we are looking forward to a good cooperation” says Jasmine Koller, Managing Director / CEO of Tool-Temp AG, Switzerland.
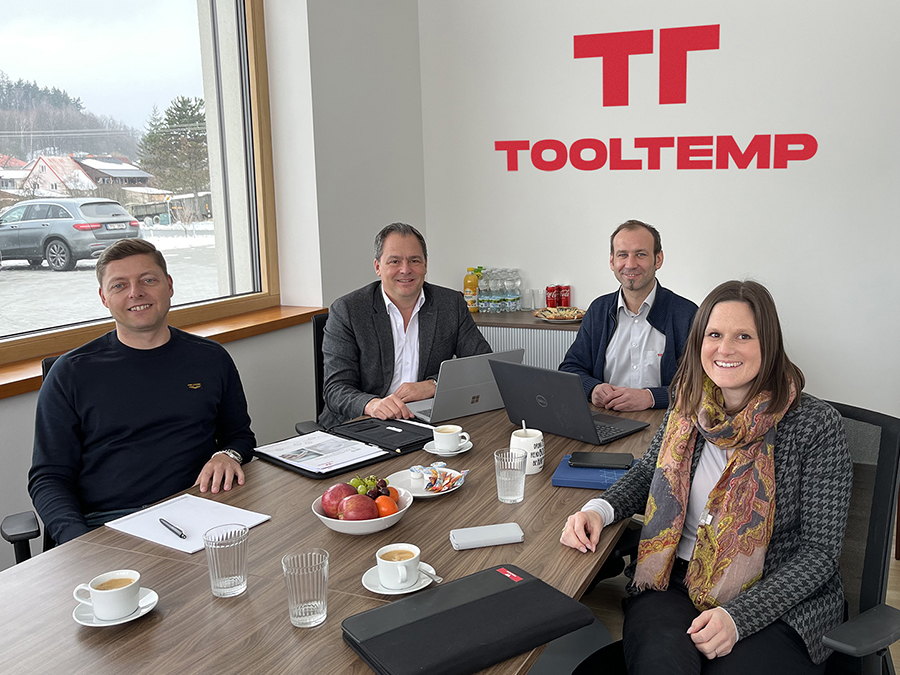
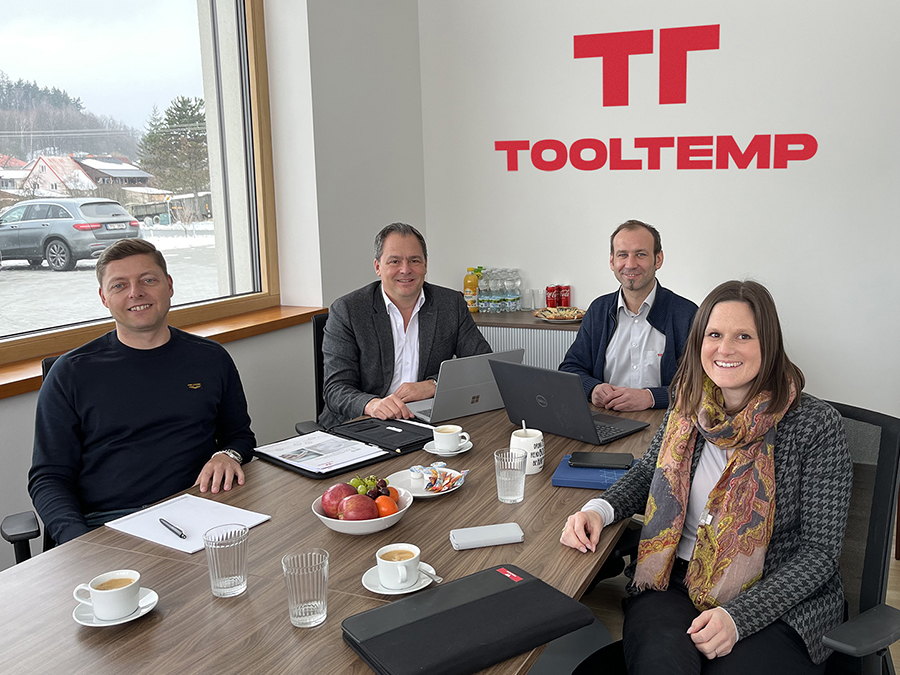
From left to right: Lukáš Devera, Marco Pellegrino, Petr Čmelík, Jasmine Koller
Tool-Temp AG at the Swiss Plastics Expo 2023
Tool-Temp draws positive conclusion from Swiss Plastics Expo 2023
Swiss Plastics Expo closed its doors again on 01/19-23 after three successful days. From January 17 – 19, 2023, the fair in Lucerne became the meeting place for all those who work with plastics and those who supply the plastics industry.
Over 4,000 visitors and 200 exhibitors found their way to snowy Lucerne. New products and solutions from a wide range of application areas were presented. Tool-Temp AG was able to present the new MATIC product line to many interested plastics processors. Numerous visitors to the booth were shown and explained how the new MATIC line of temperature control units covers all the needs of a production environment with digital networking and ensures perfect temperature control. Once again, it was gratifying to see that the future of temperature control technology is very well received in the industry.
In addition to many long-standing and well-known business partners, numerous new contacts were also made during these three days of the trade fair. The personal exchange between exhibitors and visitors was highly appreciated on both sides. “The response from interested visitors to the show exceeded our expectations and encourages us to pursue and intensify our steps into the future of innovative temperature control and cooling equipment,” said Marco Pellegrino, Chief Sales Officer.
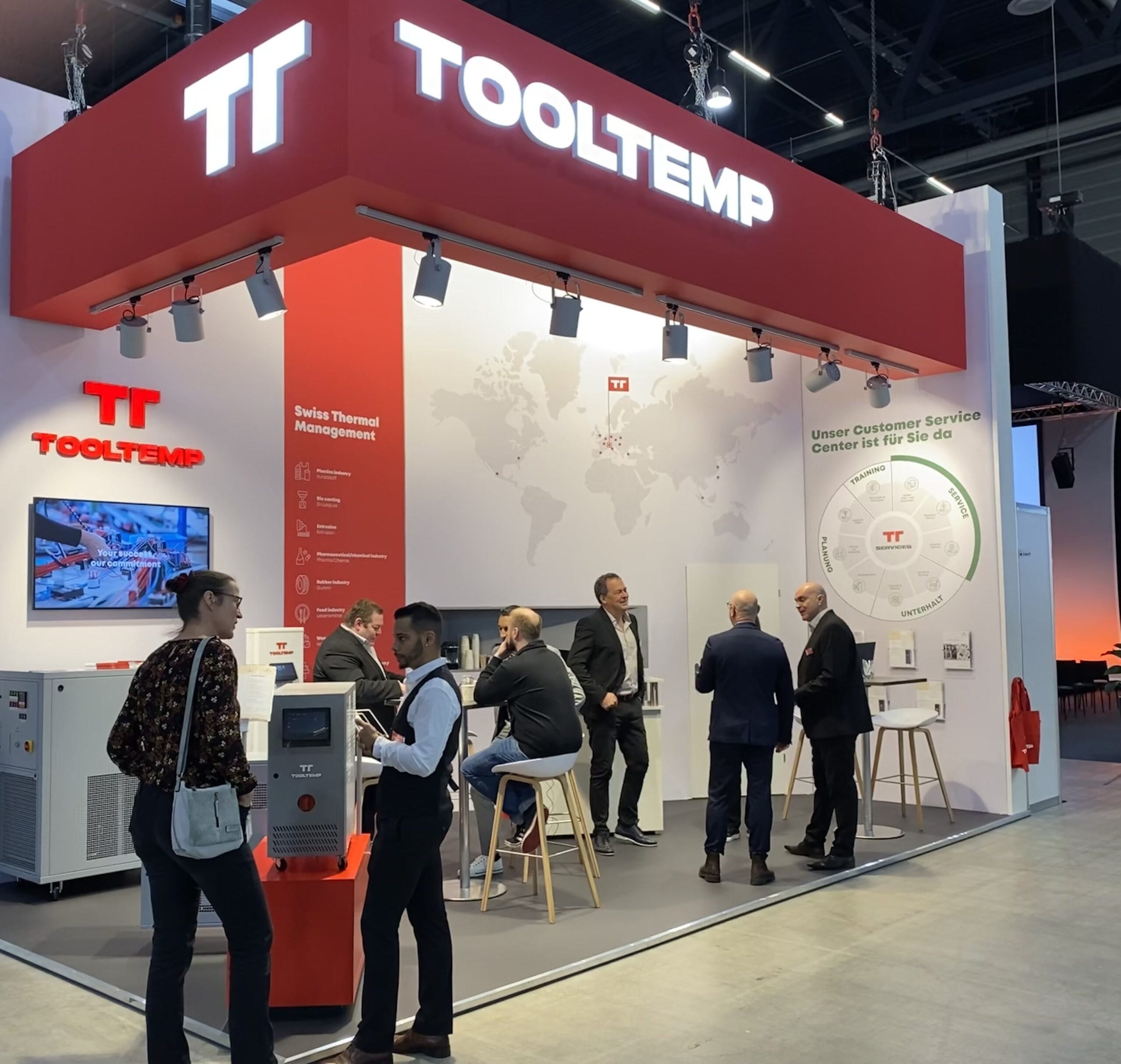
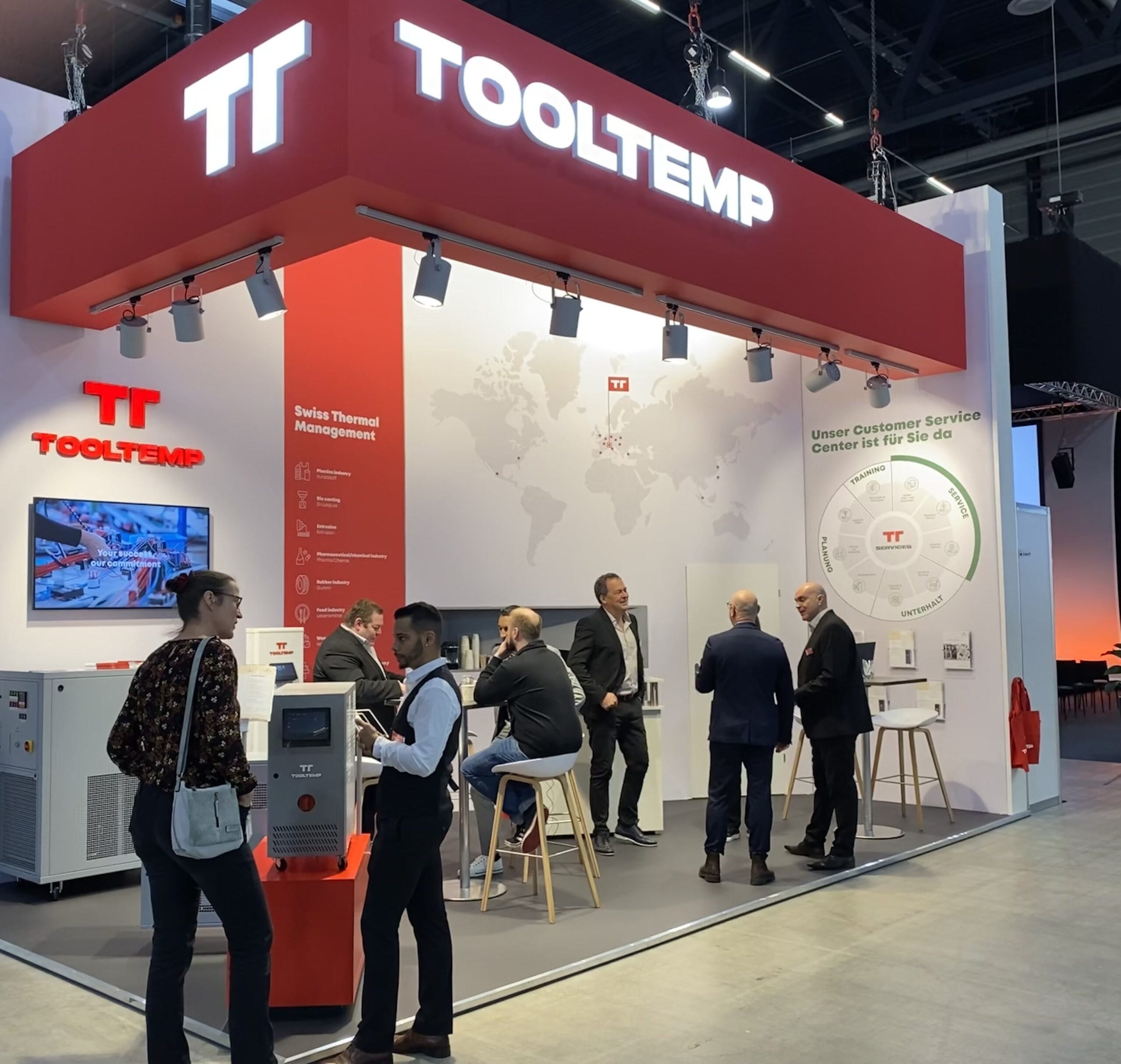
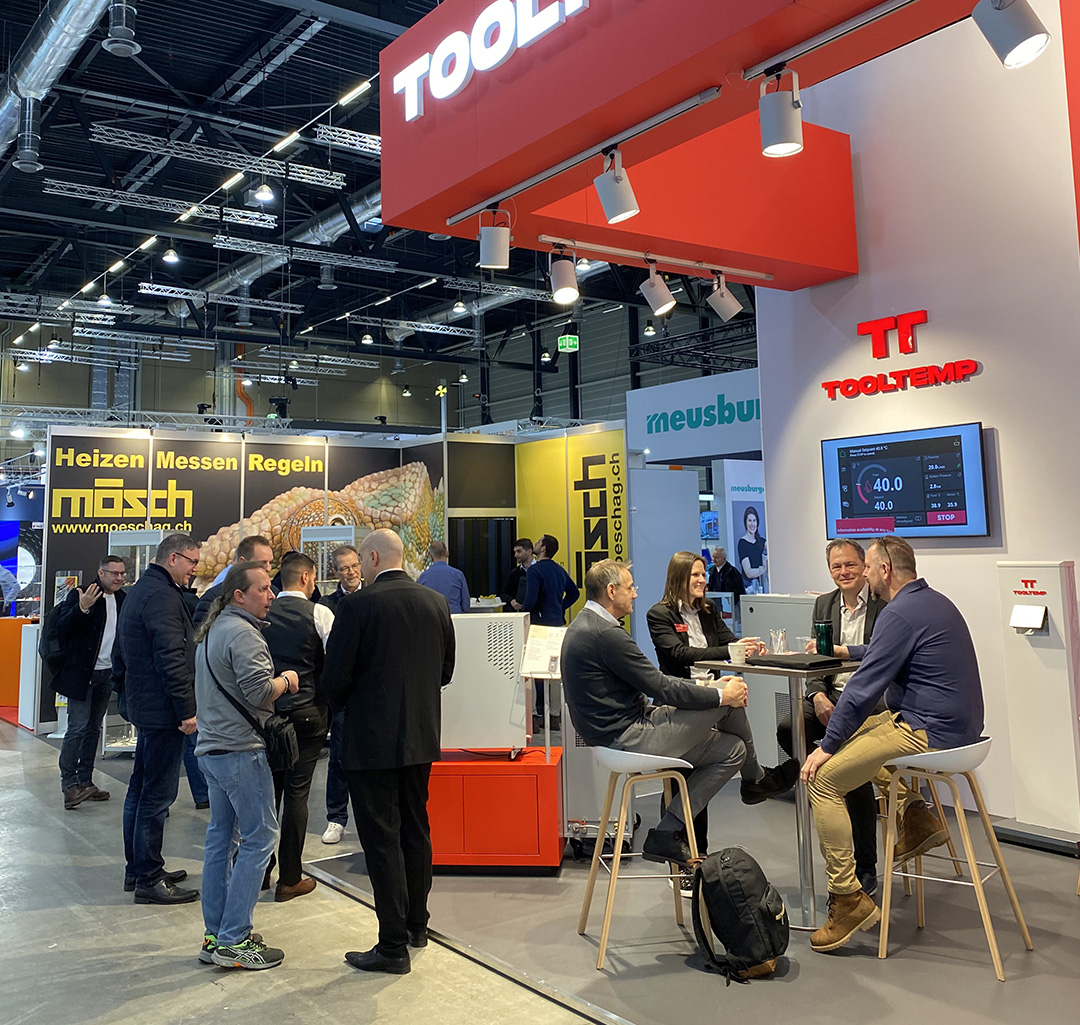
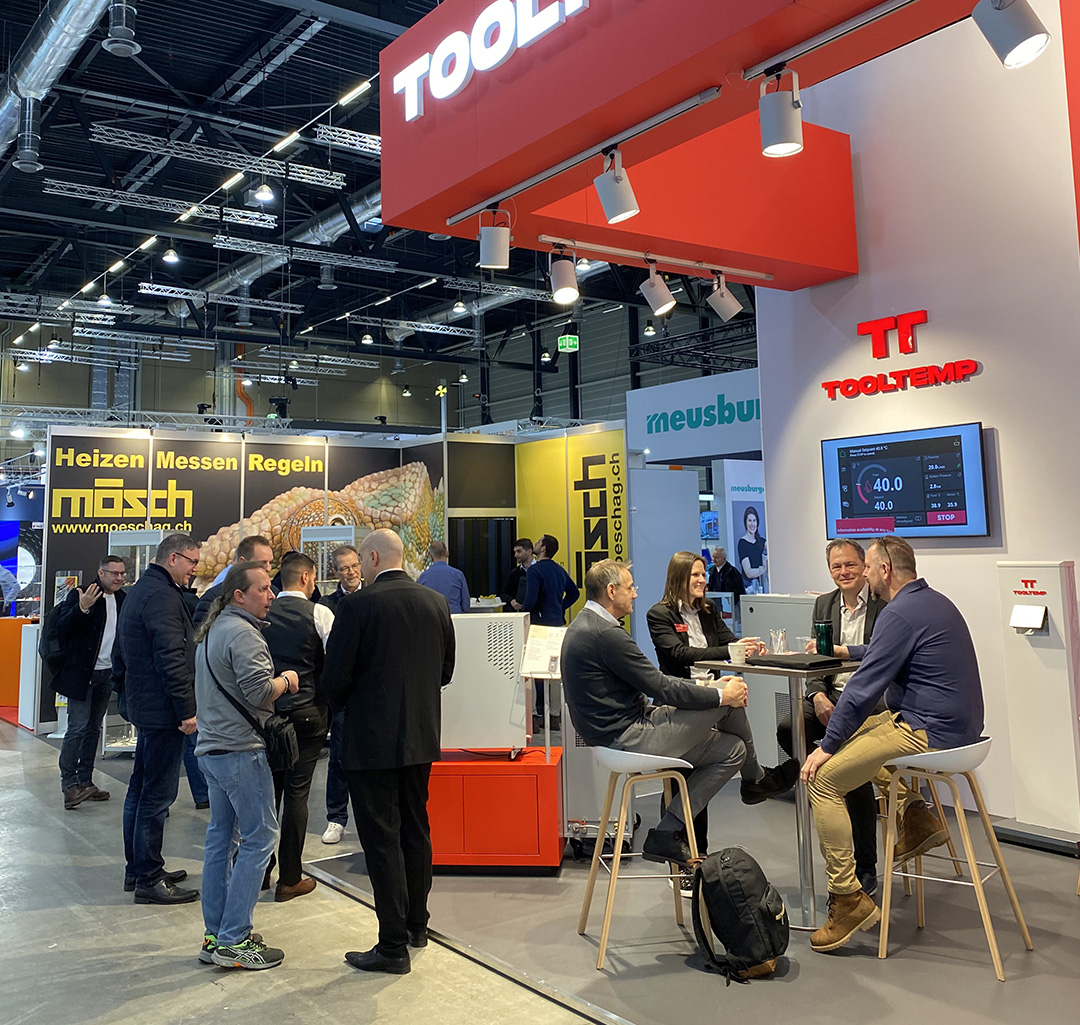
Tool-Temp on the K-2022 Conclusion
Tool-Temp draws a positive conclusion from K 2022
2,037 companies exhibited their products at the Düsseldorf Exhibition Center from October 19 to 26. 176,000 trade visitors from all over the world attended the most important industry event in the plastics and rubber industry. During these eight days of the fair, very good contacts were again made and many existing business relationships were cultivated.
Tool-Temp AG took the opportunity to present its first temperature control units from the new MATIC product line. How this new MATIC line of temperature control units covers all the needs of a production environment with digital networking was explained to numerous visitors to the booth. Tool-Temps Chief Sales Officer, Marco Pellegrino explains: “Also this year the “K” fair was a very important and successful fair for us. Once again, it became clear how great the need for smart and intelligent temperature control and cooling solutions is. Our entire product portfolio, was very well received by the many trade visitors.”
“The extremely positive response of the trade fair visitors once again exceeded our expectations and encourages us to continue investing in our innovative temperature control and cooling equipment, which is perfectly tailored to the needs of our customers,” Marco Pellegrino concluded.
Tool-Temp US, Inc. website release
We are proud to present you the Tool-Temp US, Inc. website
From a name
to a brand
In the last decade we have developed into a name known worldwide. All over the world, Tool-Temp stands for intelligent and advanced temperature control and cooling technology, developed and manufactured in Switzerland. In other words: We have blossomed into a brand. Just like our products, we want it to remain in line with the latest trends.
We have therefore decided to reposition Tool-Temp and fundamentally revise our image in 2019.
The result is impressive – today’s Tool-Temp brand embodies our core values of competence, quality awareness and international orientation. We have given the logo and the entire typography a self-image that does justice to the stature of a global brand. Our colour scheme not only reflects everything hot and cold, but also our Swiss origins. Finally, with the new visual concept we are focusing on what keeps us on the road to success – our customers, our employees, our products and our know-how.
A brand that moves with the times is a brand that moves with you. Because innovations and intelligent yet affordable solutions are the result of the wishes and needs of ambitious customers like you. And from competent creators like us. With the Tool-Temp brand, we want to be at your side for many years to come – hopefully well beyond our generation.
Logo 1973-2018
Logo since late 2019